Jan 28, 2025, Posted by: Damon Blackwood
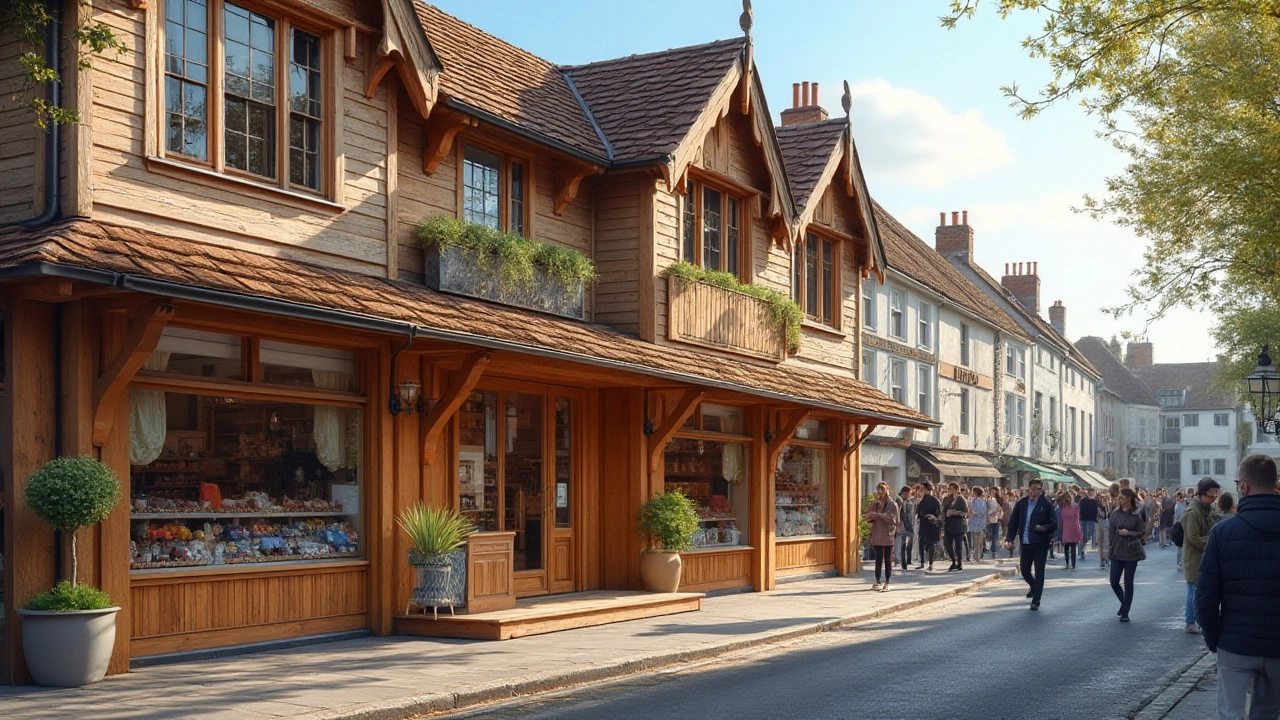
Type 5 construction is like the jack-of-all-trades in the construction world. It's known for its adaptability and affordability, mainly relying on wood and other usually combustible materials. When you walk through a quaint small-town café or browse a cozy boutique, there's a good chance you're experiencing the charm of Type 5 construction.
This approach is incredibly versatile, making it a popular choice for many small to medium commercial structures. There's more to it than meets the eye, however. From the materials used to the benefits and challenges faced, understanding Type 5 construction is key to appreciating its role in modern building practices.
Despite being made of materials that are easily found and relatively affordable, Type 5 buildings come with a set of unique advantages and safety concerns that are vital to consider. This article will guide you through the specifics of this construction type, shedding light on aspects that influence its widespread adoption in the industry.
- Defining Type 5 Construction
- Common Materials Used
- Typical Applications
- Benefits and Challenges
- Safety Considerations
Defining Type 5 Construction
Type 5 construction stands as the most flexible, one of the most abundant choices for residential and commercial buildings primarily due to its use of wood, a material that generations have relied upon. At its core, this type of construction is built almost entirely from combustible materials like wood, offering a distinctive kind of flexibility and warmth that other construction types can't quite replicate. Despite being a budget-friendly option, it doesn’t skimp on form or function. It’s a hallmark of suburban neighborhoods and commercial spaces where aesthetics and ease are key priorities. While steel and concrete can exude an industrial vibe, wood provides a more relatable and warm atmosphere perfect for places where people gather and share experiences.
Construction techniques take a modular approach, allowing free-flowing architectural ideas while maintaining structural integrity. Since the key component is wood, builders enjoy the ease of cutting and shaping it, leading to unique and creative designs. This adaptability comes into play especially in urban landscapes, where space might be limited but creativity is limitless. A quote from the National Fire Protection Association states,
"Wood framing offers a versatility for constructing buildings that other materials simply cannot match. The ease with which it can be adapted or modified makes it a preferred choice for many small to medium construction projects."
Type 5 construction is further characterized by its variety of applications, ranging from standalone properties to entire neighborhoods of twin houses or townhouses. One might wonder about the integrity and durability of such structures given their wood-based nature. Commercial buildings often embrace this construction type for small businesses or shops looking to create an inviting atmosphere.
There are specific building codes and standards that Type 5 constructions need to adhere to. This involves a balance between ensuring safety without compromising the aesthetic or functional components of a building. Wood-framed buildings are constructed with specific zoning regulations in mind, aiming to minimize issues like fire hazard risks while providing safe exits and meeting environmental considerations. According to a 2023 Building Safety Report, over 90% of houses in certain regions fall into the Type 5 category due to their cost-effectiveness and ease of assembly.
The importance of this construction type cannot be understated. Whether it’s a charming coffee shop that lures you in with a rustic charm or a small retail store showcasing elegant simplicity, Type 5 is the backbone of modern community-focused architecture. Delving into its advantages while being aware of its risks gives builders and homeowners a clear sight of how this construction type can serve their needs efficiently and safely.
Common Materials Used
In the realm of Type 5 construction, the materials used are both familiar and indispensable to many builders and architects. Wood is the primary player in this game, offering a versatile and forgiving medium that allows for intricate designs and lightweight structures. With the buoyancy of wood, developers find it easier to mold floors, walls, and supporting beams. This flexibility significantly reduces the time spent on the construction site, as wood can be pre-fabricated and then assembled on location. It's a material that doesn't just build; it constructs identities and atmospheres, offering a warm, inviting feeling inside.
Beyond wood, other commercial building materials make their appearance in Type 5 constructions. Gypsum board, also known as drywall, plays a crucial role in creating smooth, attractive interior finishes while providing some fire resistance. This sheetrock, as it's often called, is vital for non-load-bearing walls and ceilings, making it indispensable in the finishing stages. It can transform bare frameworks into visually appealing rooms that are as functional as they are stylish. The ease of cutting and shaping drywall to fit any design plan is a boon to types of construction that prioritize adaptability.
The choice of insulation is another pivotal aspect of Type 5 buildings. Typically, fiberglass and cellulose are favored due to their availability and efficiency in controlling temperature and sound within the structure. Fiberglass is often the go-to option because of its cost-effectiveness and thermal properties, which can be adjusted to suit a variety of climates and conditions. Cellulose, made primarily from recycled paper, offers an eco-friendly alternative that aids in soundproofing and draft prevention, making it an environmentally conscious choice that does not compromise on functionality.
"The materials used in lightweight construction, especially wood, provide both resilience and ease of assembly, allowing for faster project completion," explains Emily Dawson, senior architect at GreenBuild Initiatives.
The exterior finishes of a Type 5 building often incorporate materials such as vinyl, aluminum, or fiber cement siding. This choice is critical for the building's aesthetics and its durability against the elements. Vinyl siding is particularly popular because of its resistance to moisture and insects, as well as the wide array of color and texture options available. Fiber cement, on the other hand, offers sturdiness and fire resistance, proving to be long-lasting in environments subject to harsh weather conditions, though it requires a more significant investment upfront.
Fire safety is a paramount concern within Type 5 construction due to the combustibility of wood and some other materials. Consequently, the integration of fire-resistant coatings and treatments is essential. Many builders employ intumescent coatings that swell when exposed to heat, providing a protective barrier against flames. These treatments can significantly slow down the spread of fire, allowing for extra time in emergency situations. Their application ensures that Type 5 buildings meet stringent safety standards without sacrificing design flexibility or cost-effectiveness.
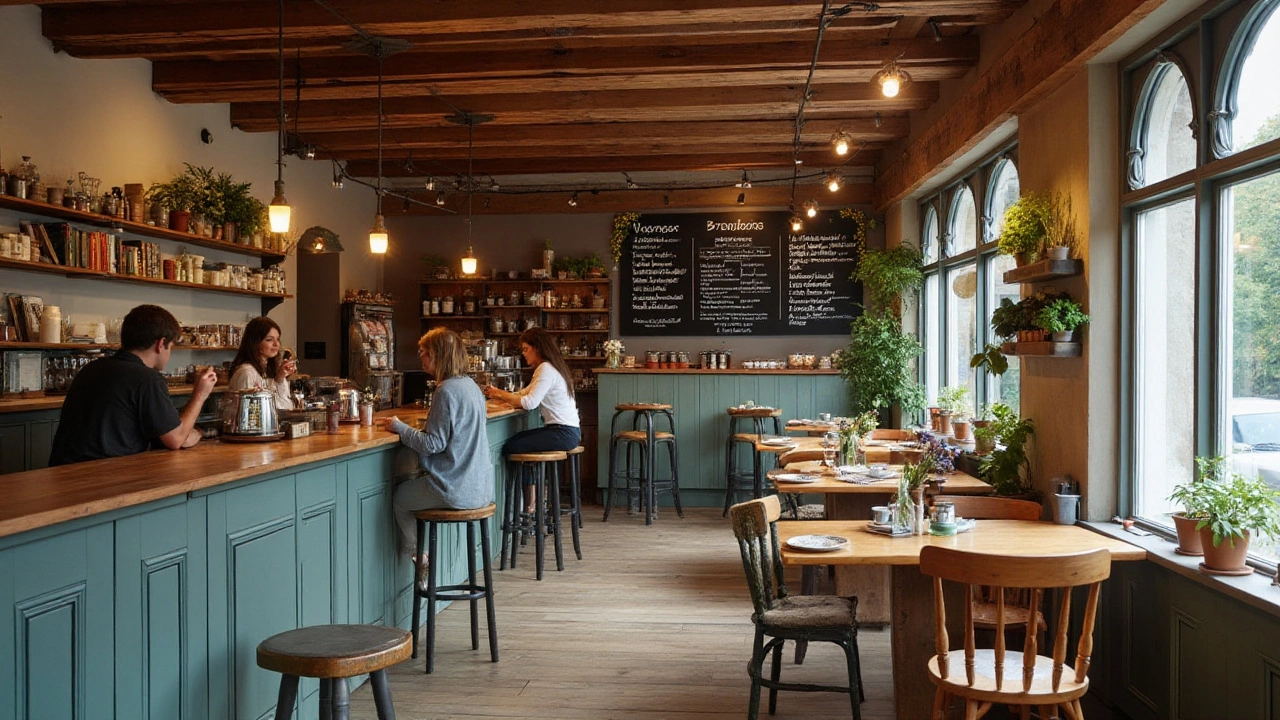
Typical Applications
Type 5 construction finds its place in the heart of many thriving communities, where small to medium-sized commercial establishments buzz with activity. These structures are often the unsung heroes of Main Street, supporting the charm and vibrancy of local economies. Given its flexibility and cost-effectiveness, Type 5 construction is a perfect fit for businesses like restaurants, retail spaces, and office buildings that need to prioritize both budget and aesthetic appeal.
In restaurants, Type 5 construction allows for creative interiors that can be easily modified as themes and trends evolve. The use of wood as a primary material not only keeps costs in check but also adds a warmth and coziness that patrons appreciate. Similarly, retail spaces benefit from the adaptability of Type 5 construction, with shops frequently redesigning to maintain a fresh and enticing atmosphere. Storefronts can transform with relative ease, allowing retailers to keep up with the ever-changing fashion and consumer landscapes.
When it comes to office buildings, particularly those housing startups or small enterprises, the open floor plans and adaptability of Type 5 buildings are invaluable. These spaces can be modified without the need for extensive and costly renovations, making them attractive to entrepreneurs looking to scale operations swiftly. Type 5’s economic advantages help align startup budgets by reducing initial investment costs, thereby promoting an encouraging environment for new ventures.
Hotels and motels, especially those outside metropolitan centers, often rely on Type 5 construction. Here, the ability to offer spacious yet affordable lodging options is vital. Since Type 5 structures can be expanded with minimal hassle, accommodating increased visitors during peak seasons becomes manageable without significant financial burden. Despite potential fire safety concerns, which are mitigated through stringent building codes and safety regulations, this construction type remains a staple in hospitality industries for budget-friendly developments.
According to the
"American Institute of Architects, Type 5 construction's efficiency in new commercial developments enhances the pragmatic allocation of resources, fostering both aesthetic and functional capabilities for small businesses."Such sentiments reflect the widespread recognition of Type 5 structures as practical yet dynamic solutions in commercial construction.
To better understand Type 5 construction's role in the commercial landscape, it's essential to recognize how it fuses tradition with innovation. Its prevalent use is a testament to the trust developers place in its flexible nature. Tables and stats from industry reports often show a higher rate of returns on investments in Type 5 structures, courtesy of their reduced construction times and adaptable designs.
Benefits and Challenges
When it comes to Type 5 construction, it's no surprise why this method is frequently chosen for commercial projects. Its primary allure rests in its adaptability and cost-effectiveness, a combination that's hard to overlook in the construction world. Using wood and other easily available materials allows builders to flex their creative muscles without shattering their budgets. Compared to steel or concrete that requires specialized skills and machinery, the methods deployed here tend to favor local craftspeople, thus boosting community economies as well. Commercial building materials often used in Type 5 projects are cost-efficient, making this approach ideal for small business owners looking for reasonable start-up costs. There's a special feeling to these buildings; they breathe warmth and creativity, often becoming the very heart of the businesses they host.
Despite the appealing benefits, Type 5 construction is not without its challenges. Fire resistance is one of the primary concerns due to the combustible nature of wood. Ensuring safety requires additional measures, such as advanced fire retardant treatments and smoke detector systems, which can offset some of the cost advantages. Modern building codes have adapted to address these safety concerns, requiring developers to meet stringent guidelines designed to minimize risk. Unfortunately, these requirements sometimes shift the balance of affordability. As architects work to incorporate safety features, the challenge becomes balancing efficiency with adherence to regulations. A quote from renowned construction expert Lucy Adams sums it up, "Type 5 structures thrive in adaptability, but their builders must think ahead - safety isn't just an add-on, it's woven into the design itself."
Construction methods in Type 5 buildings may also face environmental challenges. Wood, while biodegradable, can be subject to decay if not properly treated, and pest infestations can pose significant threats over time. In regions with extreme weather conditions, these vulnerabilities necessitate additional protective strategies. However, advancements in construction technology offer promising solutions. For instance, modern composite materials can help mitigate some of these issues by enhancing the durability of wood through engineered designs. The advent of prefabricated timber components, which can withstand harsher conditions, adds another layer of resilience. Builders now use techniques that strengthen the structure against natural elements, helping to preserve its integrity while maintaining economic viability.
In balancing benefits with challenges, it's essential to consider the lifecycle of a Type 5 structure. The potential need for maintenance and periodic upgrades** should be factored into the initial planning stages. While these buildings are highly modifiable, this very trait makes them susceptible to wear if not properly managed. Establishing a regular maintenance schedule can prevent small issues from escalating. Efficiency in design and operation remain key themes, ensuring the building serves its function without incurring unplanned expenses over time. Ultimately, Type 5 construction is about crafting solutions that embrace innovation yet respect the limits of the materials at hand.
Maintaining the goals of safety, sustainability, and affordability within commercial settings can often be a delicate balance. However, technological improvements and ongoing research continue to provide pathways that enhance the appeal of Type 5 construction. As developers strive to meet the demands of modern commerce, understanding and addressing these benefits and challenges head-on will make for a construction process that is not only successful but also future-ready.
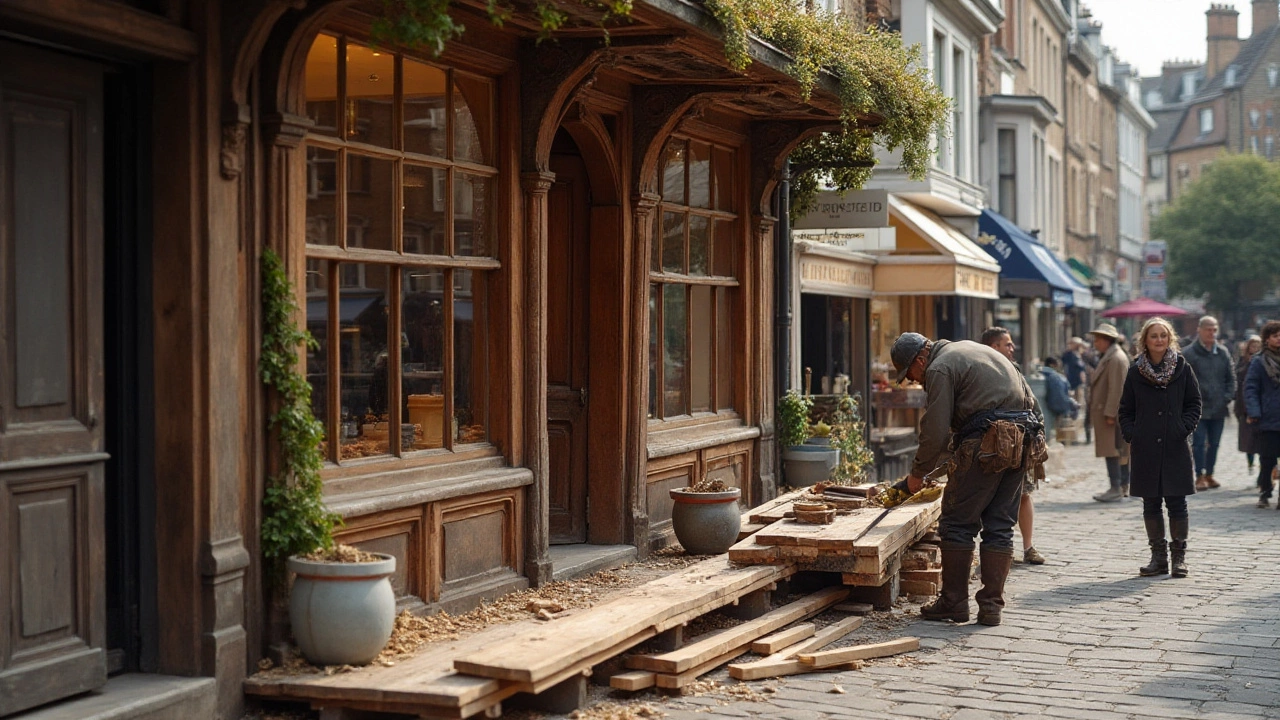
Safety Considerations
When we talk about Type 5 construction, a key aspect that often comes under scrutiny is the safety element, particularly due to its reliance on wood and other combustible materials. Wood, as endearing and easy to work with as it is, brings with it the potential for hazard, primarily from fire. In fact, one of the main concerns with Type 5 buildings is how they react in the face of fire. The materials used can ignite and burn rapidly, which may not only damage property but also endanger lives. Precautionary measures have historically focused on addressing these issues.
In recent years, advancements in fire-retardant treatments have bolstered the safety of wood structures, helping to minimize the risk. Today, numerous products are available that can effectively slow down the spread of flames. These chemical treatments are designed to alter the burning properties of wood, providing vital additional time for individuals to evacuate safely. Regulatory codes often enforce that these treatments be applied during construction. This is not just a good practice but a vital requirement in most jurisdictions.
Building codes and safety standards have evolved to keep pace with the demands of modern construction. Comprehensive fire safety protocols including the installation of smoke detectors, sprinkler systems, and alarms are mandatory in many areas. These systems play an essential role in providing an active defense against fire outbreaks. Fire separation walls, which are designed to confine fire within a designated part of a building, are also a common feature in commercial buildings constructed using Type 5 methods.
"Ensuring the safety of Type 5 constructions is not a matter of choice but necessity," emphasized Dr. Laura Greene from the Fire Safety Council, highlighting the importance of abiding by construction safety standards.
In situations where these buildings house a larger number of people, such as shopping centers or office spaces, additional safety measures may be mandated. Training personnel on evacuation protocols and conducting regular fire drills can enhance preparedness. A well-planned evacuation can be the difference between life and death during an emergency. Clear signage and unobstructed exits further contribute to ensuring that people can leave the premises swiftly and safely.
Moreover, beyond fire safety, consideration must also be given to structural stability. Factors such as wind resistance and load-bearing capacity are critical. The placement of supporting beams and the overall design should ensure that the building can withstand natural elements and unforeseen pressures without compromising its integrity. Engineers and architects play a pivotal role in examining these factors and implementing solutions that address potential risks. Adhering to engineering best practices and embracing modern building technologies has resulted in safer and more reliable Type 5 constructions.
Safety Feature | Benefits |
---|---|
Fire-retardant Treatments | Reduces flammability |
Smoke Detectors | Early fire warning |
Sprinkler Systems | Fire suppression |
Fire Separation Walls | Contains fire within a section |
Evacuation Drills | Ensures coordinated escape |
Author
Damon Blackwood
I'm a seasoned consultant in the services industry, focusing primarily on project management and operational efficiency. I have a passion for writing about construction trends, exploring innovative techniques, and the impact of technology on traditional building practices. My work involves collaborating with construction firms to optimize their operations, ensuring they meet the industry's evolving demands. Through my writing, I aim to educate and inspire professionals in the construction field, sharing valuable insights and practical advice to enhance their projects.